Document Type
Article
Version Deposited
Published Version
Open Access Funding Source
Other
Publication Date
10-7-2023
Publication Title
ACS Omega
DOI
10.1021/acsomega.3c04668
Abstract
Commercial lubricant industries use a complex pipeline network for the sequential processing of thousands of unique products annually. Flushing is conducted between changeovers to ensure the integrity of each production batch. An upcoming product is used for cleaning the residues of the previous batch, resulting in the formation of a commingled/mixed oil that does not match the specifications of either of the two batches. The existing operations are based on the operator’s experience and trial and error. After a selected flush time, the samples are tested for their viscosity to determine the success of a flush. The approach results in long downtime, the generation of large commingled oil volumes, and huge economic losses. Hence, to overcome the drawback, our work introduces a solution strategy for systematically optimizing flushing operations and making more informed decisions to improve the resource-management footprint of these industries. We use the American Petroleum Institute-Technical Data Book (API-TDB) blending correlations for calculating the mixture viscosities in real-time. The blending correlations are combined with our first-principles models and validated against well-designed experimental data from the partnered lubricant facility. Next, we formulate an optimal control problem for predicting the optimum flushing times. We solve the problem using two solution techniques viz. Pontryagin’s maximum principle and discrete-time nonlinear programming. The results from both approaches are compared with well-designed experimental data, and the economic and environmental significance are discussed. The results illustrate that with the application of a discrete-time nonlinear programming solution approach, the flushing can be conducted at a customized flow rate, and the necessary flushing volume can be reduced to over 30% as compared to the trial-and-error mode of operation.
Recommended Citation
ACS Omega 2023, 8, 41, 38288–38300 Publication Date: October 7, 2023 https://doi.org/10.1021/acsomega.3c04668
Creative Commons License
This work is licensed under a Creative Commons Attribution 4.0 International License.
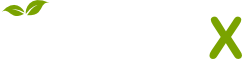
- Citations
- Citation Indexes: 1
- Usage
- Downloads: 38
- Captures
- Readers: 12
- Mentions
- News Mentions: 1
Comments
Copyright © 2023 The Authors. Published by American Chemical Society. This publication is licensed under CC-BY 4.0.