Document Type
Article
Version Deposited
Published Version
Publication Date
11-2024
Publication Title
Materials and Design
DOI
10.1016/j.matdes.2024.113428
Abstract
This paper develops hybrid steel members by integrating additively manufactured, ultra-lightweight, damage-controlled elements (DCEs) into hot-rolled structural steel members. This approach relies on segmenting a structural member into distinct sections; one or two segments are enlarged to be capacity protected; however, another end or middle DCE segment is optimized to emulate the conventional member’s strength and stiffness. A small-scale DCE was topologically optimized and then additively manufactured using a powder bed fusion technique through a direct metal laser sintering process of 17-4PH stainless steel and then was experimentally tested to study the buckling behavior under compression. The experimental testing of the optimized DCE shows a compressive strength of 81,000 times the specimen’s weight with stable post-peak buckling behavior. Numerical simulation confirms experimental results, showing a good correlation in fracture energy. A parametric study on four DCE specimens, scaled up by three, four, five, and six times, was performed and compared to hollow structural sections (HSS) of A500 Gr. C in tensile and compression strengths. The numerical simulation shows a linear relation between the weight ratio and HSS length. Additionally, numerical simulation of conventional member, DCE (scaled by three), and three hybrid members revealed that failure occurred in DCE as intended.
Recommended Citation
Farhoud, Hamdy and Mantawy, Islam, "Metal additive manufacturing of damage-controlled elements for structural protection of steel members" (2024). Henry M. Rowan College of Engineering Departmental Research. 337.
https://rdw.rowan.edu/engineering_facpub/337
Creative Commons License
This work is licensed under a Creative Commons Attribution-NonCommercial-No Derivative Works 4.0 International License.
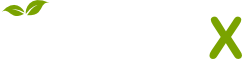
- Citations
- Citation Indexes: 1
- Usage
- Downloads: 33
- Abstract Views: 4
- Captures
- Readers: 11
- Mentions
- News Mentions: 1
Comments
© 2024 The Authors. Published by Elsevier Ltd.